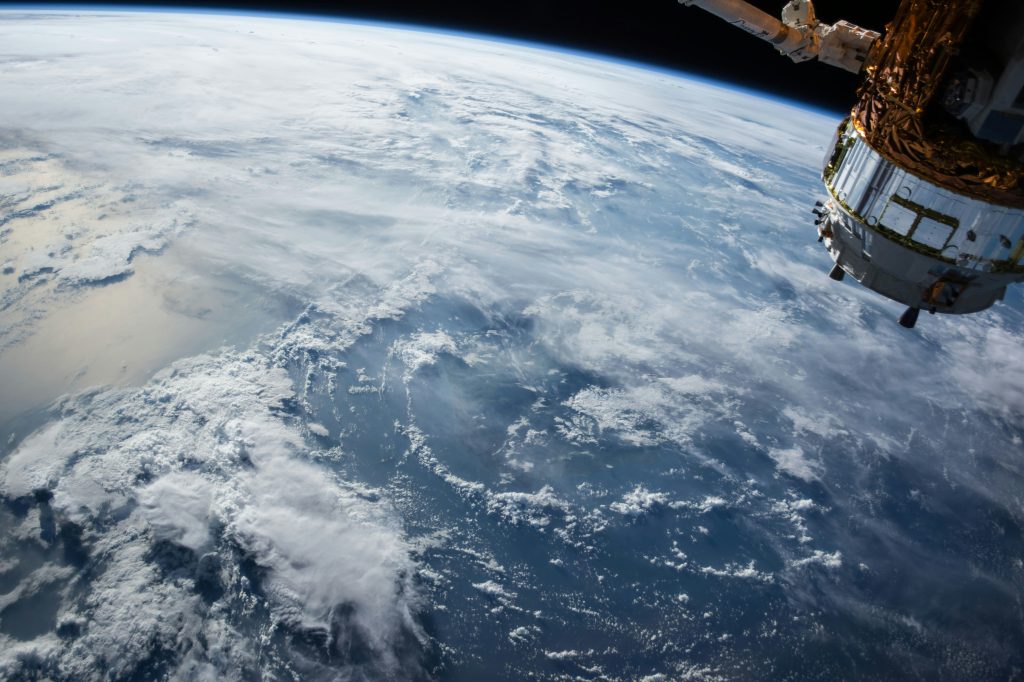
3D printing has radically changed the world of manufacturing. Its ability to create complex objects, layer by layer, and the variety of materials that can be used with this technology have opened new horizons in various production sectors.
One of the most revolutionary applications is undoubtedly the use of 3D printing in space. This technology has the potential to significantly impact the efficiency and sustainability of space missions. However, the implications of using 3D printing don’t stop here. In fact, the use of 3D bioprinters in microgravity conditions is proving crucial in the fields of rehabilitative medicine and organ transplants.
PRINTING IN SPACE: THE ANSWER TO THE SPARE PARTS PROBLEM
For each mission substantial amounts of materials are transported and stored in space to provide astronauts with everything they need to survive in orbit for long periods of time. In fact, on space stations, astronauts eat, sleep, exercise, and conduct important experiments and research.
According to NASA, over 13,000 kilograms of spare parts are stored aboard the International Space Station (ISS), and another 17,000 kilograms are on Earth, ready to be sent into orbit when needed [1].
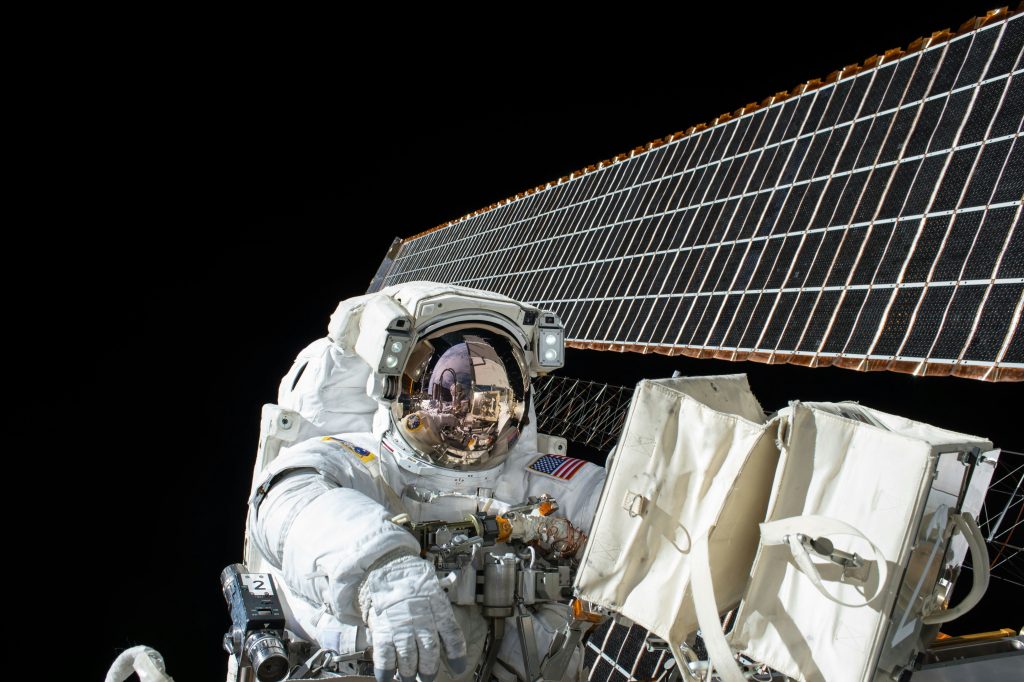
Sending parts to the ISS, 250 miles above Earth, takes time and money. That’s why, manufacturing components directly in space would significantly increase the self-sufficiency of the space station, making missions more independent from Earth.
Productive autonomy will be even more critical for far-off and more complex future missions, when assistance from Earth will be impossible. 3D printing is undoubtedly the technology that best guarantees productive autonomy, thanks to its fundamental role in the spare parts production.
THE FIRST 3D PRINTER IN SPACE
The first installation of a 3d printer dates back to 2014, with the launch of an FFF printer marked “Made In Space” (now a company acquired by Redwire Corporation) on the International Space Station (ISS). The project goal was to allow astronauts to manufacture spare parts and useful tools on-site if necessary. Launched on September 21, 2014, the printer produced the first 3D-printed piece on November 24 of the same year – the front plate of the printer’s frame.
The first functional piece was instead a ratchet wrench. The .stl file is available on the NASA website.
PRINTING IN MICROGRAVITY
The project wanted to test the printer in a microgravity environment to assess the feasibility of in-orbit production and to study the effect of the lack of gravity on the characteristics of 3D-printed parts. As hoped, the research on the samples didn’t reveal significant differences between these pieces and those traditionally printed.
PRINTING METALS
After the first experiments in space, NASA has continued its research over the years, testing new and more advanced 3D printers and various types of plastic materials. Despite the significant progress, a decisive breakthrough has not yet been achieved for 3D printing of metal components.
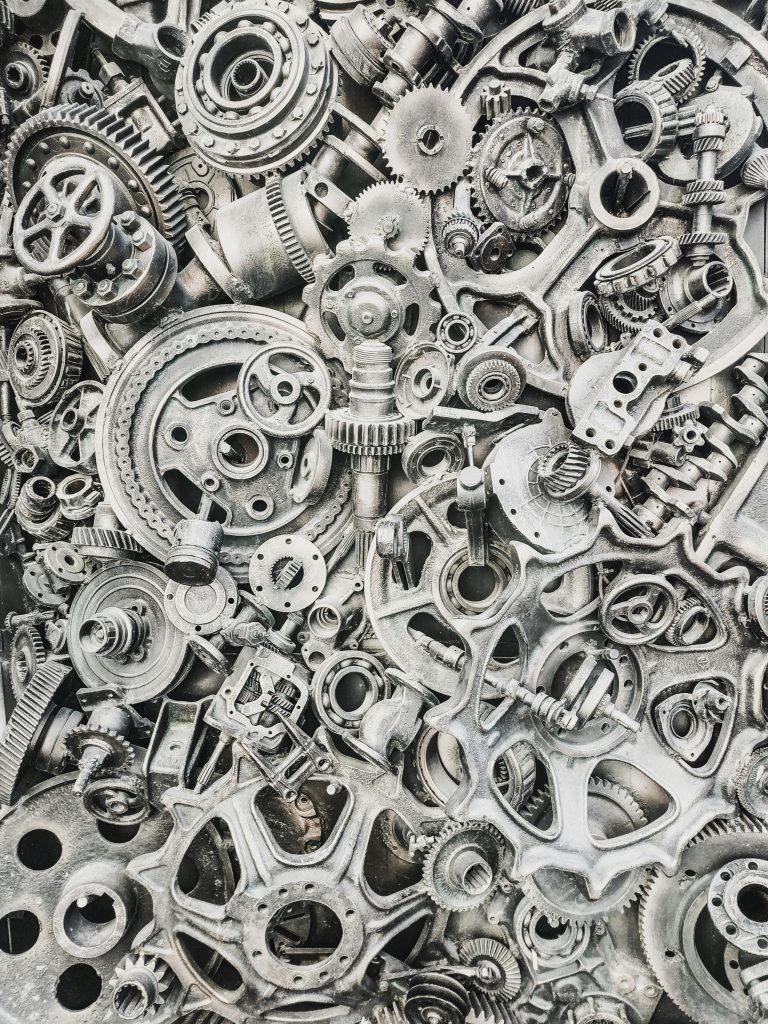
On Earth, the most widely used additive technology for metals is Selective Laser Sintering (SLS). This technology uses a laser beam to sinter powder particles. In space, using this technology is more complex due to the flammability of the powders, potentially harmful to airways if inhaled. However, the urgent need for metal parts for space missions is driving space agencies to identify new solutions that can work safely on the International Space Station.
3D PRINTING HUMAN TISSUES IN SPACE
Among the most interesting applications is the use of 3D printers to create human tissues, cells, and organs. The ability to print bio-inks in microgravity conditions could significantly revolutionize the fields of regenerative medicine and organ transplants.
The first experiments began in 2019 with the launch of the first American bioprinter, the BFF (3D BioFabrication Facility), to the International Space Station (ISS). The goal of the research conducted by ISS astronauts was to reproduce human tissues in microgravity conditions.
THE FIRST AND SURPRISING RESULTS: THE FIRST 3D-PRINTED MENISCUS
The real breakthrough came in September 2023, after the launch of the new and updated version of the BFF in November 2022. ISS researchers successfully bioprinted a human meniscus in 3D using live human cells as bio-ink. The decision to print a meniscus was due to its anatomical characteristics, which makie it easier to reproduce than other human tissues. Cartilage is, in fact, poorly vascularized, making it easier to print.
According to John Vellinger, Executive Vice President at Redwire, this is a revolutionary milestone with significant implications for human health. The Centers for Disease Control and Prevention (CDC), in fact, estimates that 75,000 Americans are on the organ transplant waiting list each year. In Italy, at the same time, according to the National Transplant Center [2], over 8,000 patients are waiting for an organ transplant.
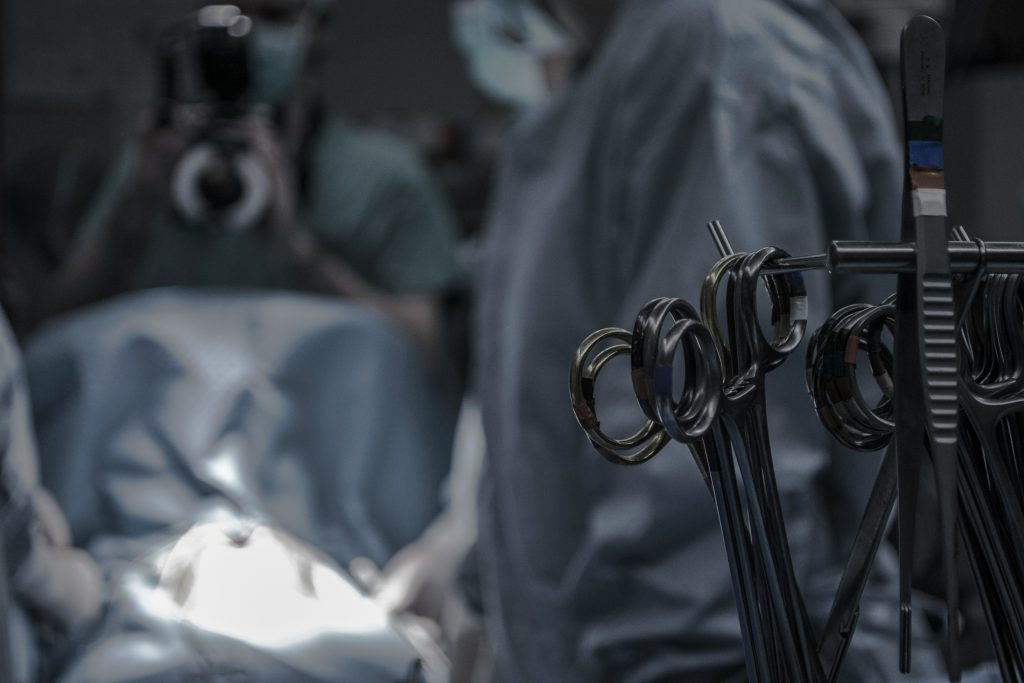
For its next investigation, Redwire aims to print a sample of cardiac tissue [3].